Dismantling any type of heavy industrial equipment is always a massively complex undertaking – but when it comes to decommissioning nuclear power plants, the challenges are exponentially greater. In addition to planning exactly what pieces of equipment will be worked on in what order, the process is complicated by the limited amount of time workers can spend within the plant itself to minimize their exposure to radiation. Using hands-free mobile scanning with the NavVis VLX system, virtual reality solution provider eSite has developed unique workflows to aid engineers working on nuclear decommissioning projects across Europe. Combining rapid reality capture with virtual reality, eSite has redefined what is possible for both safety and efficiency in the nuclear industry.
Mobile Mapping Process Designed to Meet Unique Safety Challenges
The process of decommissioning a power plant that contains nuclear materials is both complex and uniquely hazardous. In any plant there can be areas that have higher levels of radiation exposure than others – and the overarching principle for working in those areas is to perform the work in as little time as possible while keeping distance and shielding from radiation sources (ALARA– principle, ‘As Low As Reasonably Achievable’). The principle of maintaining exposure time “as low as reasonably achievable” is a cornerstone of safety in nuclear industry : the less time you spend in controlled areas, the better – from cost and safety perspective.
With new build projects, doing this complex planning with detailed 3D models is easier, but for the older plants which are being shut down across Europe, no such 3D models exist. For an environment in which time is a critical element, the traditional terrestrial laser scanning process has clear disadvantages – the field work is slow and during it you make contact with the plant structures. The scanning experts may not have clearance or training to enter critical areas, and they are also adding to their own personal risk of exposure.
NavVis specializes in scanning equipment and software designed for rapid and accurate capture, and last year released the NavVis VLX system, a shoulder-mounted scanning device designed for work in difficult, tight, or uneven environments, as well as providing hands-free access. By integrating the NavVis VLX into nuclear decommissioning workflows, Fortum’s eSite has been able to improve dramatically the safety and speed of the reality capture of nuclear power plant structures, systems and components, and this way provide plant workers with valuable 3D environments that they can use to plan their tasks. This saves money and reduces the radiation dose of workers.For mapping in challenging environments such as nuclear power plants, SLAM scanning (Simultaneous Location And Mapping) has become a sweet spot between accuracy and speed because of its ability to self-reference and locate even while moving. While not as accurate as static scanners in all conditions, the SLAM scanning enables a continuous scan via a walkthrough with more than an appropriate level of detail. Combined with a more user-friendly process that requires less training to deploy, SLAM scanning workflows have the potential to drastically reduce the amount of time needed to capture indoor spaces.
Reality Capture Workflows that Optimize Time, Safety and Security
Founded in 2019 as a service unit of Fortum, eSite is an industrial Virtual Reality solution provider who are no strangers to complex environments of plants, factories and construction sites. For example Fortum Nuclear Services is using eSite in the first nuclear decommissioning project in Finland, decommissioning of the FiR 1 nuclear research reactor. Working safely in the nuclear industry is a key concern, for obvious reasons, and nuclear safety in Finland has been improved continuously for more than 40 years.
By creating realistic 3D point cloud models from reality capture of areas due to be decommissioned next, an extra layer of safety can be created. Because the time spent by field operators performing decommissioning tasks at the field needs to be minimized, it is paramount that the work procedures they follow are both efficient and correct – something that can have an increased likelihood to succeed if rehearsed in virtual reality created through reality capture, says Miko Olkkonen, head of eSite.
“Having a room or an area that needs to be decommissioned in a nuclear plant means that you need to go in there, cut some pipes that once had radioactive water, and you need to do it safely . This also means that you need to do everything to make it as fast as possible and as safe as possible with the lowest radiation dose.”

Field work at nuclear power plants require careful planning. (Courtesy of Fortum)
When planning the work procedures virtually it is possible to refine them to be completed quickly and accurately, avoiding radiation hot spots. Every action taken in the controlled area of the facility means time spent being exposed to radiation. The principle, “as low as reasonably achievable” drives each of these choices. When combined with other sensors that can also map radiation, an overlay of radiation hotspots can be augmented into the visualizations – helping to identify risky areas ahead of time.
“We can do the reality capture in the morning, process it for the afternoon, put the scan into virtual reality glasses, and the field operators can practice the work they need to do for a 15 minute cut of the pipe. In virtual reality, you can practice where you walk, what you do, where you keep your equipment. You can practice to do to it faster, with fewer steps, avoiding hot spots. Of course the environment changes during the decommissioning and the advantage is that you can discard the initial reality capture, and the next time you need to perform work in that location you take a new reality capture of that moment,” says Olkkonen.
From Years to Minutes
Inside Finnish nuclear power plants, where Fortum Nuclear Services and eSite operate, there are radioactive areas and rooms that are accessible to people only for few days per year during the nuclear power plant’s annual outage. During these few days, hundreds of maintenance tasks are performed with a minute accurate schedule.
The best practice for a decade has been to go in to these areas and perform stationary laser scanning. This has enabled planning for next year’s outage tasks during the operating phase of the plant, though the areas are not physically accessible. Even with 10’s of hours of scanning work, we have been able to capture only limited sections. Each moment spent in these controlled areas increases the radiation dose of the survey team. In 2015, to improve the coverage of the scan and to reduce received dose, Fortum began capturing these areas with 360 photos and video. This reduced the time of field data capturing from 10’s of hours to few hours. Though this technique reduced dose, it didn’t allow for measuring distances in all places nor extracting 3D information vital for the planning and engineering for outages.
Today, new mobile reality capture technologies like the NavVis VLX have reduced the field work time in these challenging areas even further – from many hours to about forty-five minutes, cutting the dose received even further into one third from earlier. Now by combining stationary laser scanning, 360 videos and mobile reality capture data from the NavVis VLX, eSite has found the sweet spot for extensive scanning coverage, highly accurate measures, photorealistic images and all this captured with the lowest time reasonably achievable. For the nuclear industry, this means concrete added value: lower dose, shorter outages and improved safety. And this is something that eSite and Fortum are able to provide for the nuclear industry with their global nuclear reality capture services.
If you are a nuclear power plant owner, outage contractor or work in nuclear decommissioning get more nuclear specific reality capture reference cases and white papers from Fortum Nuclear Services www.fortum.com/esiteview-nuclear
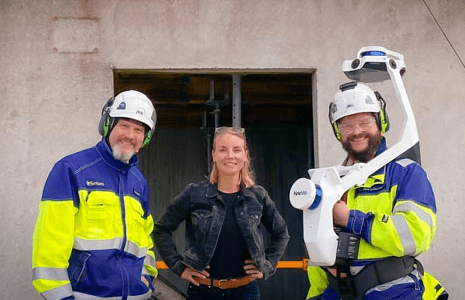
eSite and NavVis verifying the VLX performance in field tests during summer 2020. (Courtesy of Fortum)
The scans in nuclear power plants themselves are planned for weeks in advance, allowing them to be performed only once and in the shortest time possible. For especially sensitive areas eSite works with plant personnel who have the appropriate knowledge, access and training to go in and do the capture even themselves.
The unique form factor of the NavVis VLX allows for hands-free operation, which can enable personnel to perform other tasks or measurements alongside the scans, and avoids contact with any surfaces while the scan is taking place. Rolling cart-driven scanning systems were prone to picking up nuclear contamination from the floors of the plant, and would sometimes require special decontamination or even disposal after the project was done. Walking through the same room with the VLX on a workers’ shoulder minimizes the amount of contamination that accumulates on the equipment – this saves time and reduces decontamination costs.
The procedures followed in working in nuclear facilities have evolved over time, each time striving to define what is “reasonably achievable” – minimizing time and maximizing safety. With the bar being raised by these procedures, the repercussions may resonate throughout the nuclear industry, says Olkkonen.
“There’s an interesting twist: now that it is reasonably possible to do reality capture in nuclear power plants – the industry should do it. The bar for ‘reasonable’ has gone down, which means the safety has gone up.”
Beyond the nuclear industry, the same techniques and workflows can be readily applied to other safety critical and heavy industry – including oil and gas and other power generation plants. Anywhere that could benefit from limiting the access of people to hazardous areas or having a virtual model to practice work procedures, plant owners can drive costs down across the board while maintaining and even improving safety.
Scan at unprecedented speeds, without compromising on quality. Meet your project requirements with the most accurate mobile mapping systems on the market. See how NavVis delivers >