Nordic Unmanned is a Norwegian provider of Remotely Piloted Aircraft System (RPAS) services. The company has delivered tailor-made drone solutions to more than thirteen European countries and is currently the only publicly listed drone operator in Europe. The company’s Staaker family of products are all produced at the company’s workshop in Sandnes, Norway. The drones are designed to perform in harsh, Nordic climates.
Recently, Nordic Unmanned introduced the Staaker BG-300 Railway Drone, that can inspect critical parts of the railway infrastructure whilst driving on the track. When the Railway Drone encounters oncoming traffic, it can avoid dangerous situation by flying to the side of the track and let traffic pass. The sensors onboard the drone automatically detect changes on the railway, whilst providing a live data feed to decision makers.
Covering more ground in less time
The Railway Drone was created in collaboration with a railway owner based on use cases identified by their employees. The Railway Drone is a cost-effective alternative to existing solutions, as it covers more ground in less time, and reduced the need for downtime on the railway track to conduct maintenance. The Railway Drone offers consistent data collection, without the need of downtime on the railway track, which ultimately lowers the cost of data collection, improves the quality and efficiency of data acquisition, resulting in higher uptime for the rail service providers.
The Railway Drone can fly both day and night, dependent on the customers wishes and local authority regulations. Maintenance in the railway industry is generally done at night when there is less traffic or on some occasions no traffic at all on the inspected rail section. Some owners may choose human surveyors, whilst others use maintenance wagons equipped with sensors, which may require manual power for motion. In some cases, rail maintenance may use a train equipped with sensor to conduct similar maintenance. However, independent on the method of inspection, current operation demands mobilization of large amount of equipment and manpower.
System endurance and operation
The Railway Drone can operate on the railway for around 7 hours with an average speed of 20 km/h. The drone can cover up to 200 km, which is a distance equivalent from Amsterdam – Brussel. Furthermore, it can switch from one railway track to another, give way to oncoming traffic, and switch to alternative tracks. With the ability to not disturb regular traffic, the Railway Drone will significantly streamline and improve the maintenance work at railways.
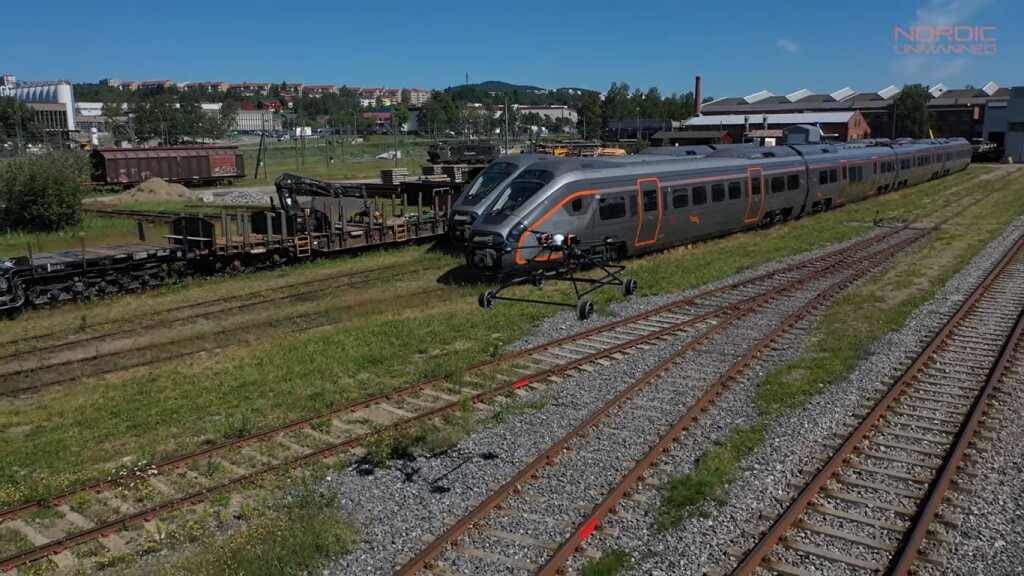
The endurance will be dependent on the combination of wishes of the customer: because rolling along the tracks requires less power than flying, the amount of flying has an impact on the amount of "driving” time. The Railway Drone is a modular system with both a flying and no flying versions. There are also different energy modules (batteries/hydrogen) which may be used according to user’s endurance and flight requirements. The launched version requires supervised piloting, and when it comes to driving, it works with manual control and/or waypoint navigation.
Providing a live data feed to decision-makers
The sensors on board the robot automatically detect changes on the railway, while providing a live data feed to decision-makers. The live streaming consists of camera footage. The change detection is presented after analysis as you need data from previous or similar operations to compare to. To clarify, the data is processed by Nordic Unmanned before being sent to the end customer and decision makers. The final visualization software is still under testing and design.
At current technology maturity, the commercialized Railway Drone requires assisted flight control. Automatic and autonomous systems are already developed but require more testing to reach commercial maturity. In addition, for a fully automated capability, the Railway Drone requires an integration to the railway traffic system. This will be a standardized integration in the future.