The directors of Bloom Technologies, Dan Arnold and Anu Rastogi, believe 3D scanning is lagging behind. They say that if you look at a typical terrestrial laser scanner, you’ll see that the electrical components, battery consumption, and embedded operating systems haven’t changed much over the years. 3D scanning software hasn’t fared much better. “The thing we notice about the scanning industry, generally, is that there is a lot of legacy stuff,” says Arnold.
BloomCE, the company’s flagship software product, is a point cloud engine designed to buck the trend.
In addition to looking contemporary, and including a number of modern programming touches, BloomCE does more than the “point cloud polishers” that you’re used to. Sure, it offers web sharing, annotation, measurement, and collaboration functions, but it’s also a design and construction tool uses point clouds as a drawing primitive. That means it allows you to select and manipulate point cloud objects as if they were part of a digital photo, or CAD objects. That means it can also offer an integrated environment for extremely fast viewing and editing of CAD data alongside your as-built point cloud data, and perform clash detection from point cloud to point cloud, point cloud to CAD, and CAD to CAD.
How does it offer all these functions?
A New Perspective on the Point Cloud
During a demo of the software, Arnold told me the team “took a very different view of the point cloud data that resulted in some real differences in our products.”
Most legacy point cloud products, he explains, are wedded to the bubble view. This means they structure point clouds as gridded spheres that radiate from the locations where the scans were captured—click on a scan location, and you’ll see the point cloud visualized as a sphere that surrounds you like a bubble. Arnold says this was necessary when the software was originally developed, due to the limited computing power available. It also makes point clouds cumbersome.
Arnold explains that BloomCE reads this data, and restructures it into a Cartesian coordinate system. This means they are spread in even intervals across the space depicted in the file. This structure, which Bloom calls a “point field,” is much easier to work with.
Arnold explains the value of this process by telling me to think of modern photo processing. Many higher-end cameras can shoot in an uncompressed RAW format, he says, but you wouldn’t post a RAW file on your website because it’s too large. You would tinker with it, and then convert it to the much smaller JPEG to post.
Think of BloomCE as doing something similar to your point clouds.
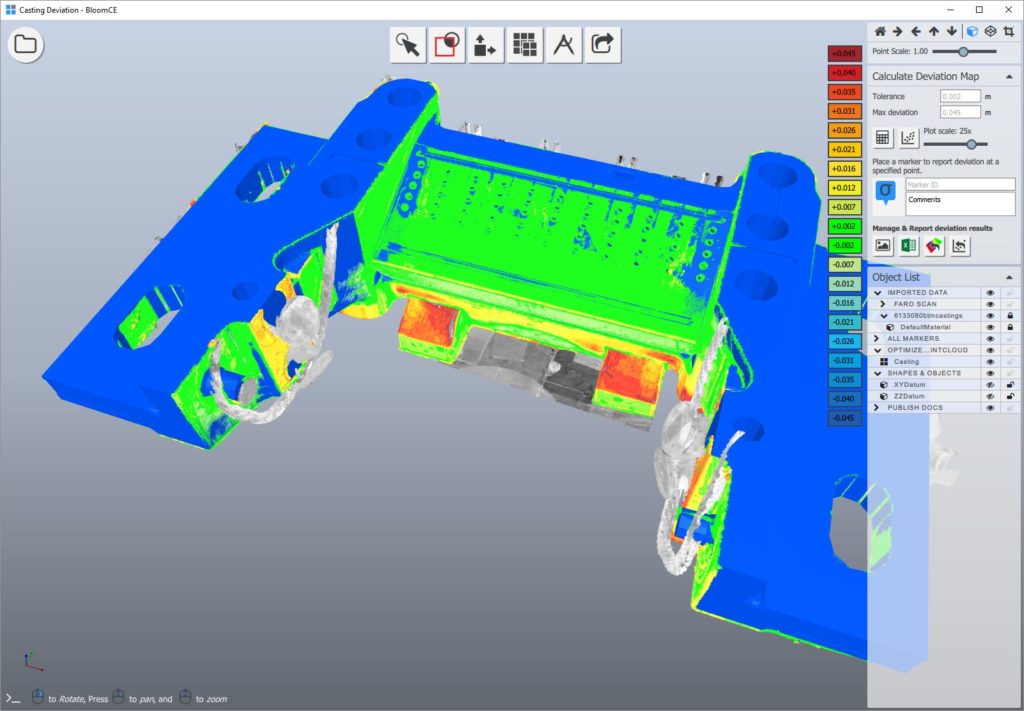
Performing a deviation analysis of a large machined part by registering the design model to the as-built point cloud.
Faster, Easier
This enables you to do to novel things with your data. After the registration stage, you can upload your final files to BloomCE’s web sharing service in a matter of seconds. If you’re a scanning professional, you can quickly take a cross-section of the file—only the pertinent section—and send it to an engineer who can review it on her mobile phone, or download to perform her design work.
Once that engineer has the file, she can manipulate it like a 3D photograph. BloomCE includes tools like brushes that select an object like a pipe without selecting any of the points in its vicinity. That means you can cut, copy, or drag the pipe around like a piece of a digital photo. In other words, you can treat point cloud objects like CAD objects—without going through the hassle of reverse-engineering or meshing them first.
CAD and As-Built, Together at Last
BloomCE’s unique processing method enables clever CAD integration. You can view your as-built point cloud data alongside your CAD design data, in a single environment. Where many applications will register point clouds to point clouds, BloomCE will also register point clouds to CAD, and CAD to CAD, all in the same application. That means it offers deviation analysis and clash detection from point cloud to point cloud, but also point cloud to CAD, and CAD to CAD.
BloomCE also offers direct integration with CAD programs, allowing you to move point clouds or CAD objects back and forth easily for comparison and updates.
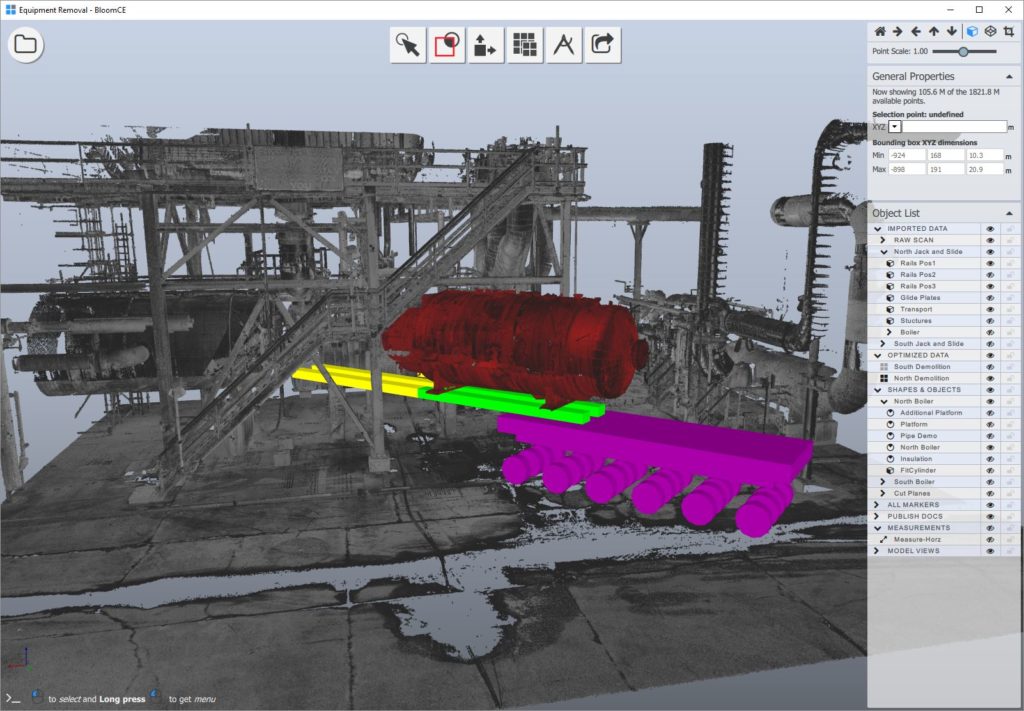
Equipment removal, planned in BloomCE.
Value, Illustrated
Arnold offers a use case to demonstrate the software’s versatility. He pulls up a file of a refinery, explaining that the site was captured so the owner operators could move a large boiler. “The question is, how do you get it out of there?”
He starts by using the brush to select the pipes and insulation that need to be removed to make way for the pipe, and simply deleting them. Next, he selects the boiler with the brush and uses a transform tool to lift it 18 inches. He reminds me that he is still working with the point cloud—no modeling involved.
Next, he says, the engineers would use CAD to model the rails and plates needed to move the boiler, and then simply place them next to the boiler in BloomCE. “So, next, we can use keyframe animation to show how we would lift it up, do a diagonal move, a rotation, reposition it, and glide it into place on the truck.”
Arnold said the engineering client showed this same animation to the owner operator, who said “yes, you can do this, my building is not going to fall down. No one is going to get killed and it’s not going to hit the columns.”
The comments Bloom got back from their client were enlightening. “If they were to go model it in a CAD system,” Arnold explained, “there was always this question if it is modeled correctly. But when they look at this point cloud data, there’s eight billion points there—if one of the scans has poor registration or distortion it shows up right away. When they look at this data, they have a high degree of confidence that that’s the way the condition is.”
Big Potential
Arnold showed me how BloomCE can be used to update a point cloud file to reflect any demolition performed. Simply select with the brush and cut the demolished portions from the file. Now, you can perform clash detection without generating false clashes against objects that don’t exist anymore.
He showed me how you can compare point clouds of a utility room to find what has been added and what has been removed between scans, or how you can register a point cloud to a CAD model to perform quick deviation analysis on a machined part, or to inspect a cement floor for flatness. He showed me how you can perform clash detections between different CAD files and import the pertinent section of the point cloud to AutoCAD to make updates.
As much as Arnold showed me (and it was a lot) he told me the software does a much more. BloomCE is developed to be a design and construction tool that uses points as a drawing primitive to enable easy manipulation, and brings as-built data and design data into a single environment for you to compare and process. In other words, it’s made to be fast and flexible. What you use it for is up to you.
To find out more about the application, visit the website here.