CONTENT SPONSORED BY BENTLEY SYSTEMS
Large infrastructure projects face communication problems, and the A9 Dualling program faced more than most.
This £3 billion Scottish government project will update 177 kilometers of the A9 between Perth and Dundee by 2025, widening it from a single carriageway to a dual carriageway to facilitate economic growth and safer travel. CH2M and Fairhurst are developing a 43 km section of this project as a joint venture, with both firms participating in design and supervising construction.That 43 km stretch of road also happens to run through a beautiful and remote part of Scotland that is under national and international environmental protections—including the Cairngorms National Park, the largest national park in Europe.
Completing this work successfully requires regular, clear, and informative communication with landowners, business owners, and other members of the public concerned about the environmental impact of the project. Facing these challenges, the CH2M and Fairhurst Joint Venture (CFJV) knew it needed a better way to facilitate communication and understanding for a wide variety of stakeholders.
The Solution is 3D Meshes
CFJV used a range of Bentley software applications—including Bentley Descartes, OpenRoads, OpenBridge Modeler, and ProjectWise—to generate and manage numerous design options for the A9. But specialized infrastructure tools like these aren’t always ideal for communicating with the public, so CFJV decided to test Bentley’s ContextCapture.
Using this application, the team processed over 276 orthophotos to create a 3D reality mesh with 54 gigapixels of resolution . Since they had the foresight to use ground-control points as benchmark, the mesh hit an accuracy of 3-5 cm. This enabled the team to match the mesh against the DTM used for the original design options, and even lay those design options directly on top of the mesh using MicroStation.
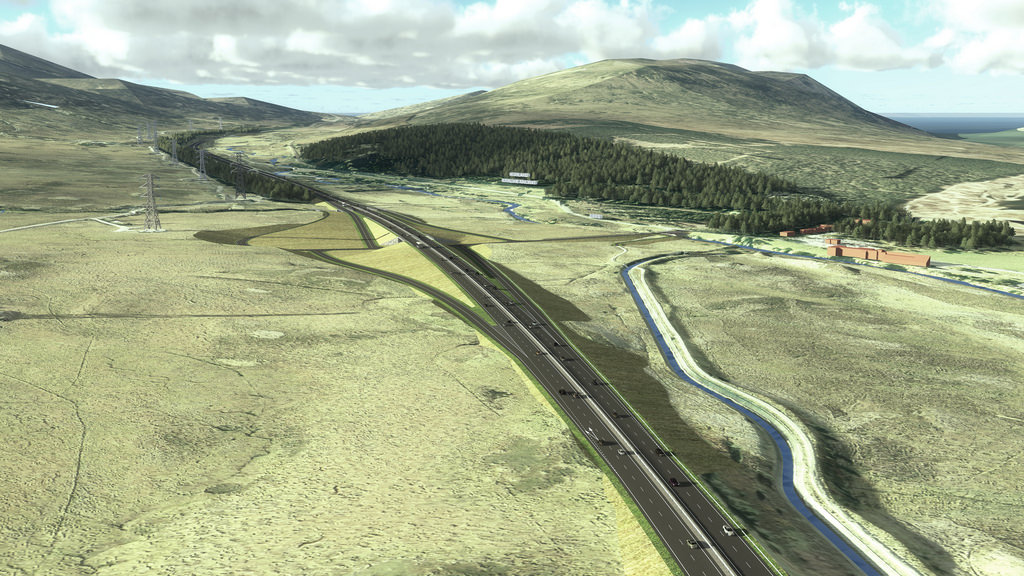
The detailed 3D reality mesh enabled much better stakeholder communication across the board.
From there it was easy to export the data to Bentley LumenRT and create interactive 3D visualizations intuitive enough for anyone to use.
But CFJV had another smart idea. Rather than load every design option into its own Bentley LumenRT LiveCube visualization, they combined every option into a single LiveCube so the viewer could select the options they wanted to see. That enabled the user to switch between a number of possibilities for junctions, mainline, bridges, and even toggle a switch to turn the existing terrain on and off.
Better Public Communication
The geometric accuracy and environmental realism of the 3D models helped CFJV to communicate their plans clearly and effectively. In public forums and private client meetings, engineers pulled up the model, and rotated, zoomed, and panned to show how the different design options would look in their real-world context.
Using these 3D models, CFJV was able to respond to questions like, “Can you show me the view from my home?” “Can you show me what the bridge would look like from this vantage?” “How are you minimizing the impact on this particular stretch of land?”
Better Team Communication
In addition, CFJV found that the interactive 3D model facilitated communication among the teams working on the project as well.
The design team used Bentley LumenRT to export executable file versions of the models, which they sent to contractors or clients. Any of these stakeholders, whether they had Bentley LumenRT on their machines or not, could open the file to interact with the designs and see everything the engineers did. With this rich 3D information, miscommunications among distant stakeholders were reduced significantly.
CFJV was also able to put the 3D model on a web server, which one project manager began to use as a basis for showing his team the changes he wanted made. He grabbed screenshots, marked them up, and sent them to his team by email. The interactive 3D model offered him a quick way to explain complex operations with little effort.
In the past, when a group like CFJV would have used 2D technical drawings, renderings in complex design software, or even 3D flythroughs, this kind of communication and efficiency simply would not have been possible.