At YII2017 in Singapore, Bentley made a number of announcements about their portfolio of products–as usual. But the big news was that there was no big reality modeling news.
Back up, let me explain: No longer a novelty, reality modeling has become an expected part of any built-world project. Bentley users have adopted it enthusiastically, turning their attention beyond simply capturing 3D information, and toward using it downstream—as a means for gathering, indexing, and sharing a wealth of information about physical assets.
This year’s Be Inspired awards were a pretty good example. Overall, 111 of the nominated projects used reality modeling tech—over 62 last year. The finalists in the reality modeling category, which I judged, were a pretty good example of this development (the Penn project being a sentimental favorite of mine).
What’s more, Bentley announced a number of partnerships this year built on reality modeling tech. Two of those partnerships—with Siemens and Bureau Veritas—are using Bentley’s ContextCapture technology for what CEO Greg Bentley would call “continuous survey” of physical assets. In other words, they are creating a continuously updating digital model that reflects the state of the real-world asset.
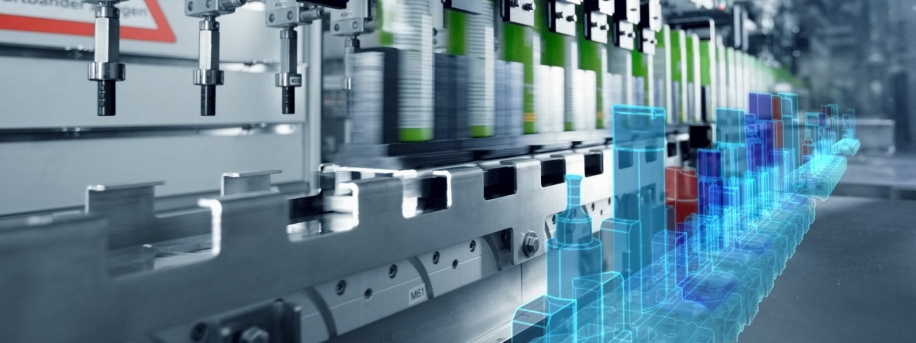
Courtesy of Siemens
Siemens and the digital twin
As with Topcon, so too with Siemens: Since partnering, Bentley and the German industrial manufacturing company have been enmeshing their cloud services “to advance their respective users’ strategies in going digital.” In practice, this means the two companies are aiming to help asset owners better connect reality modeling data like meshes and point clouds with their engineering models and ubiquitous sensors for better operational efficiency.
Siemens’ global head of IT Helmuth Ludwig dug in further as he explained the “unprecedented opportunity that ubiquitous connectivity brings for assets with digital engineering models that incorporate both their physical and functional characteristics.” Siemens has a familiar name for these hybrid digital engineering models: the digital twin. And it’s not just for manufacturing.
During his keynote presentation, Ludwig detailed a workflow to illustrate the idea. A team captures a process plant in its “as-operated state” using ContextCapture and photography, then links this digital twin to the IoT-enabled components using Siemens’ MindSphere IoT operating system. Now, the 3D reality model is an easy to use visual index of the plant’s current state. Navigate, click, check up on different components without going to the plant itself. This particular plant was able to check on a malfunctioning motor, for which they designed and 3D printed new parts.
The same logic, Ludwig argues, can be applied to larger assets—like smart cities.
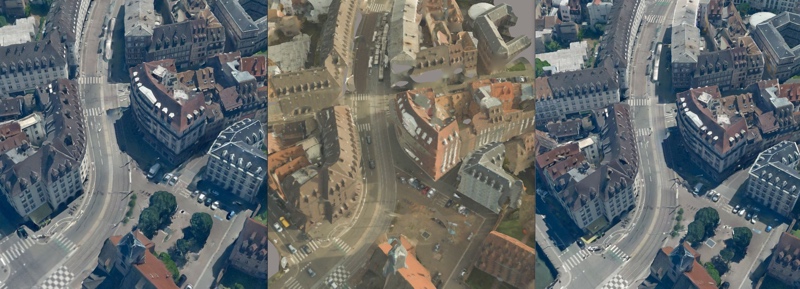
A ContextCapture reality mesh comparing photogrammetry, lidar, and a hybrid input. Image courtesy of Bentley Systems and City of Strasbourg
Bureau Veritas and the digital clone
But how do you get a twin without setting it up yourself? Make a clone! That’s what Bureau Veritas’ partnership with Bentley promises.
The French company, founded in 1828, performs lab testing, inspection, and certification services. With its new “digital cloning” service, the company will capture an asset for you using Bentley’s ContextCapture technology, and generate a digital twin.
Why use BV to do this instead of doing it yourself? The company’s pitch is that they can verify the model matches reality, they can capture more efficiently by gathering detailed data only where needed, and they’ll process it for you. Essentially, BV is now a 3D capture service provider.
But with a twist. BV says they’ll classify the parts of the asset one at a time and connect them to the owner’s data. They’ll update the data as necessary. They also promise to exploit machine learning and image recognition, which will help find and classify problems, like corrosion, in terms of severity and impact—so they can find problems, and send inspectors only where the problems are.
Suffice it to say, 3D capture is now inextricably woven into the fabric of infrastructural operations, and becomes more important to the built environment every year.